By GMM News | 2024-07-12 | Global Partner News |
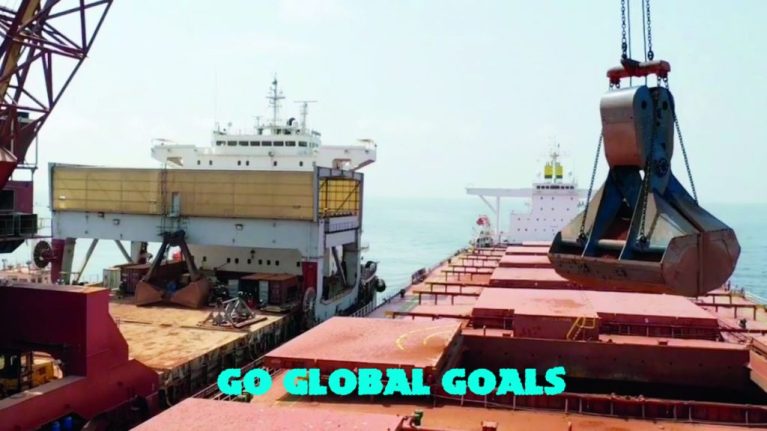
SMT Shipping is a leader in the global maritime industry and has many years of experience with transshipment in the shallow shores of the West African region. Market transitions led them to this grab selection challenge. The solution had a significant impact: a 25% productivity boost, and it paid back over four times its cost in the first year.
The Challenge: The search for the optimal crane and grab combination
To stay profitable, SMT Shipping needed to optimize their transshipment operations. The company owns and operates vessels with high-loading capacities and shallow drafts, allowing them to transport significant amounts of cargo from terminals, often located in rivers, to the open sea. Once there, they use large cranes to transfer the cargo to Cape-size vessels. For these rapid transfers, an efficient grab is essential. Marc Smeets, Technical Project Manager at
SMT Shipping, explains, “We need to optimize the continuous cargo transfer process to maximize our profit.”
Transitioning from Bauxite to Iron Ore
Originally,
SMT’s vessels in West Africa transferred bauxite with a Nemag scissors grab that already improved their productivity. However, when the bauxite market collapsed, they shifted to transfer iron ore for a client in Sierra Leone. This posed a new challenge as the specific gravities of bauxite and iron ore differ significantly. Bauxite is 1.6 tonnes per cubic meter, while iron ore is heavier at 2.5 tonnes per cubic meter. SMT Shipping found that their three existing grabs were not optimal for the heavier iron ore, leading to slower grab cycles and crane overloading.
The Solution: Enabling a higher efficiency rate with the Nemax grab
Faced with suboptimal equipment, SMT Shipping needed a new grab specifically designed for iron ore. Nemag introduced the NemaX grab, which promised enhanced efficiency. Unlike traditional clamshell grabs, the NemaX requires significantly less wire to operate, saving valuable time on each cycle. Marc Smeets recalls, “Saving seconds on each cycle doesn’t seem much until you calculate the impact on an annual basis.”
Nemag’s initial presentation highlighted that the NemaX grab showed a productivity improvement of 14% to 19% compared to other grabs. These numbers convinced SMT Shipping to invest in the NemaX grab, seeing its potential to improve their overall efficiency.
The Results: 25% productivity boost, three months ROI and easier maintenance
The NemaX grab’s integration into SMT Shipping’s operations led to impressive results. Initially, the crew needed time to adapt to the new equipment, but within the first month, the handling rate increased from 1,000 to 1,250 tonnes per hour. This represented a 25% productivity boost compared to the previous Nemag scissors grab, which wasn’t optimally suited for iron ore.
The NemaX grab not only improved productivity but also enhanced safety and maintenance efficiency. With fewer moving parts than traditional grabs, it significantly reduced the risk of breakdowns and made maintenance easier and faster.
The introduction of the NemaX grab resulted in a 25% productivity increase, a three-month return on investment period, and easier maintenance. Making it a pivotal asset for SMT Shipping.
Future plans and the next steps
After seeing the success of the NemaX grab, SMT was interested in buying another grab to increase their productivity even further. The new grab includes custom SMT adjustments and a unique feature allowing weight adjustments, making it versatile for both wet and dry ore handling. Another tailored innovation to improve their flexibility and overall performance with a hybrid grab.
Any car can get you from A to B. However, only some cars offer both reliability and performance. The same goes for grabs. But more importantly, don’t bring a road car to a Dakar rally. Use the right grab for the right job, as SMT did.